3D打印(yìn)技術及軍事應用有怎(zěn)樣的使用(yòng)前景分析
點擊(jī)量:484 發布時間(jiān):2017-05-03 作(zuò)者:草莓视频ios(上海)增材製(zhì)造(zào)技術有限公司
增材製造(zào)技術是對傳統切削加(jiā)工技術的原理(lǐ)性顛(diān)覆,不需要(yào)傳統的模具、刀具、夾具及多道加工工序,在一(yī)台設備上可快速而精密地製(zhì)造出任意(yì)複雜形狀(zhuàng)的零件,從而實現“自由製造”,解決了許多過去難以實(shí)現的複雜結構零件的製造問(wèn)題,因此在(zài)武器裝備研製(zhì)生產中顯示出不可替代的作用和(hé)廣闊應用(yòng)前景,成為(wéi)世界國防前沿技術的研究熱點和重點。美國《時代(dài)》周刊已將增(zēng)材製(zhì)造技術列為“美國十大增長最快(kuài)的工業”,英國《經濟學人》雜誌則認為它將與其他數字化生產模式一起推動實現新(xīn)的工業革命。
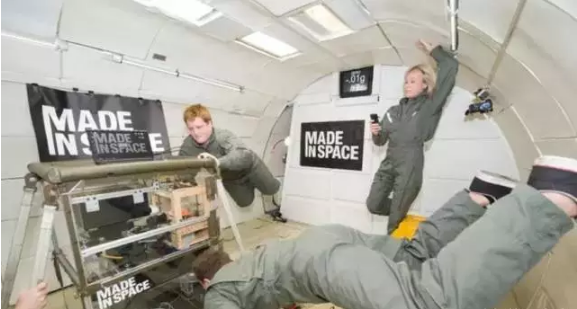
(一)研究(jiū)進展
近年來,增(zēng)材製造技術持續升(shēng)溫,世界許多國家(jiā)均通過製定製造(zào)業發展戰略、製定技術路線(xiàn)圖等多種措施,促(cù)進(jìn)增材製(zhì)造技術的發展和應用。
增材製造工藝過(guò)程檢測技術取得(dé)重要進展,成形效率和質量顯著(zhe)提高(gāo)。近(jìn)年來,隨著工藝過程不斷優化,適用材料品種不斷增加,設備加工檢測能力不斷提升(shēng),製造效率、產品精(jīng)度和質量(liàng)獲得穩步提升,增材製造技術應用範(fàn)圍迅速擴展。2013年,DST Control公司利用熔融堆積成(chéng)形技術成功製造了(le)COLIBRI微型高性能光(guāng)電萬向支架中的(de)20個塑料零件,該光電萬(wàn)向支架用於無人係(xì)統的成(chéng)像,並已裝備一個球形地麵無人車Groundbot。預計COLIBRI支架最初的年產量為50個,交貨周期由(yóu)10-12周減少(shǎo)到4周。2016年,Promolding公司通(tōng)過利用Stratasys PolyJet 3D打印解決方案,將注塑模具(jù)的(de)生產時間縮短了93%,空客公司(sī)等航空航天製造(zào)企業(yè)也有望大規模應用這一技術。
增(zēng)材製造技(jì)術的標準規範日益完善,標誌著該項技術開始走向成熟應用。目前,增(zēng)材製造(zào)技術標準與規(guī)範的製(zhì)訂日益受(shòu)到重視,將促進該技(jì)術(shù)的健(jiàn)康持續發展。2012年,美國材料實驗協會(ASTM)國際委員會針對Ti-6Al-4V的增材製造製訂了F2924-12標準。2013年9月,美(měi)國國(guó)家標準與技術(shù)研究院(NIST)公布了總額740萬美元的資金援助(zhù)項目,以解決增(zēng)材製造在測量和標準(zhǔn)方麵麵臨的重大問題。2015年7月,歐盟“增材製造標準(zhǔn)化支持行動(SASAM)”項(xiàng)目(mù)發(fā)布了增(zēng)材製造標準化路線圖,明確闡述了標準化對增材製(zhì)造技術發展(zhǎn)和應用的重(chóng)要性。
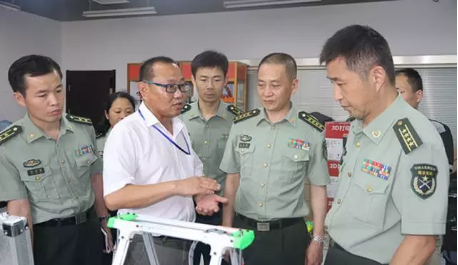
增材(cái)製造技術和生物製造技術深(shēn)度交叉融(róng)合,疊加優勢效應開始顯現。生物3D打印能直接打印出活體組織,甚至直接打印活體替代器官。2010年6月,美(měi)國Organovo公司成功研製出“按需打印”患者所需的人體活器官的機器,對未來戰場及時救援具有巨大潛在意義。2013年2月20日,美國康奈爾大學的研究(jiū)人員利用(yòng)牛耳細胞3D打印出(chū)人造耳朵。2016年,美國(guó)海軍研究實驗室(NRL)化學部(bù)門負責人Ringeisen發明的生(shēng)物激光(guāng)打(dǎ)印機(jī)(BioLP)目前已經獲得專利批準,美國海軍研究實(shí)驗室希望借(jiè)此技術治療一些常見戰場傷病(bìng),如創傷性腦損傷、燒傷以及聽力損(sǔn)傷等。
(二)發展趨(qū)勢
增(zēng)材製造技術代表著生產模式和先進製造(zào)技術發(fā)展的趨勢,產品(pǐn)生產將逐步(bù)從大規模製造向定製化製(zhì)造發展,滿足社會多樣化需求。其間接作用(yòng)和未(wèi)來(lái)前景難以估量。增材製造優(yōu)勢在於製造(zào)周期短、適合單件個性化需求(qiú)、大型薄壁件製造、鈦合金(jīn)等難加工易熱成形零件製、結構複雜(zá)零件製造。增材製造技術相對傳統製造技術還麵臨(lín)許多新挑戰,還存在使用成本高(10元/g~100元/g),製造(zào)效(xiào)率低(dī),例如金(jīn)屬材料成形為100g/h~3000g/h,製造精度尚不能令人滿意;其工藝與裝備研發尚不充分(fèn),尚未(wèi)進入大規模工業應用等問題。目前,增材製造技術還隻是傳統大批(pī)量製造技術的一個補充,未來將會與傳統(tǒng)技(jì)術優選、集成,形(xíng)成新的發展增長點。
向功能零件製造發展。采用激光或電子束直接熔(róng)化金屬粉,逐層堆積金屬,形成金屬直接成形技術。該技術(shù)可以直接製造複雜結構金屬功能零件,製件力學性能可以達到鍛件性能(néng)指標。隨(suí)著(zhe)技(jì)術的不斷成熟,增材製造的使用成本(běn)不斷降低,其應(yīng)用重(chóng)點(diǎn)已經由最初的設計和原型工具(jù)的應用,轉(zhuǎn)向了(le)功能部件和(hé)產品的生產,進一步提高(gāo)精度和性能,同(tóng)時向陶瓷零件的增材製造技術和複合材料的增材製造技術發展。
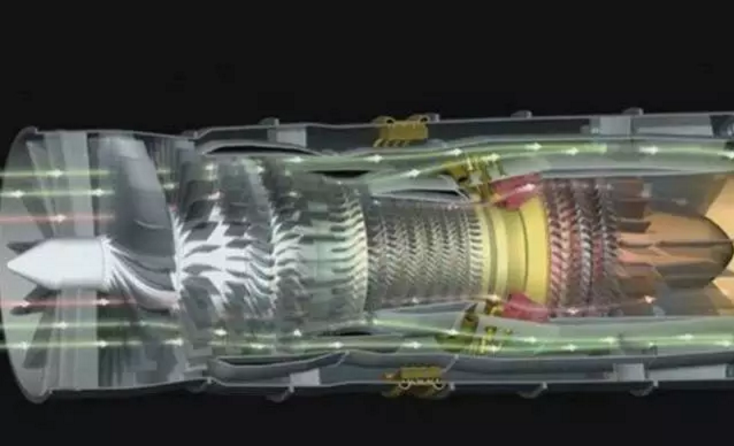
向智能化裝備發展。目(mù)前,增材(cái)製造設備在軟件功(gōng)能和後處理方麵還有許多問題需要優化。例如,成形過程中需要加支撐,軟件智能化和自(zì)動化需要進(jìn)一(yī)步提高(gāo);製造過程,工藝參數與材料的匹配性需要智能化(huà);加工完成後(hòu)的粉料或支撐需要去(qù)除等問題,這些問題直接影響設備的使用和推(tuī)廣。
向組織與結構一體(tǐ)化製造發展。增材製造下一步是實現從微觀組織到宏(hóng)觀結構的可控製造。例如,在製造複合材料時,將組織設計製造與外(wài)形(xíng)結(jié)構設(shè)計製造同步完成,在微觀到宏觀尺度上實現同步製造,實現結構體的“設計—材料—製造(zào)”—體化。支撐生物組織製造、複合材料等複(fù)雜結構零件(jiàn)的製造,給(gěi)製造技術帶來(lái)革命性(xìng)發展。
(三)重大影響
增材(cái)製造技術可顯著(zhe)改(gǎi)善裝備製造流(liú)程,提(tí)高裝備的戰術(shù)適應性,不僅(jǐn)將為(wéi)裝備研製帶來重大變革,而(ér)且(qiě)可能(néng)從根本上影響國防工業基礎,甚至會對戰爭形態和作戰樣式產生顛(diān)覆性影響。
增材製造將實現複雜裝備輕質、高強、低成本及敏(mǐn)捷化(huà)質的飛躍。目前,使用3D打印鈦合金(jīn)零件的F-35已經進行了試(shì)飛。據估計,未來如果(guǒ)3000多架戰機都使用增材製造技術生產零部(bù)件,不僅大大(dà)提高“難產”的F-35戰機的部署速度,而且還能節省數十億(yì)美元成本,如原本相當於材料成本1~2倍的加工費現在隻需原來的10%。
增材製造可大幅降低貴重資源消耗,實(shí)現國防(fáng)稀缺資源高效利用。采用增材製造方式超過90%的原材料可以回收(shōu)再利用,這對於(yú)國防工業的稀缺資源來說,具有重要的戰略(luè)意義。例如在(zài)航空航天領(lǐng)域,為(wéi)實現零件的高性能,需要大量使用鈦合金和鎳基合金等昂貴的戰略材料。F-22戰機的鈦合金框材(cái)料利用(yòng)率僅為4.8%,如運用增材製造技術,可節約2/3以上的昂貴鈦合金原材料(liào)。
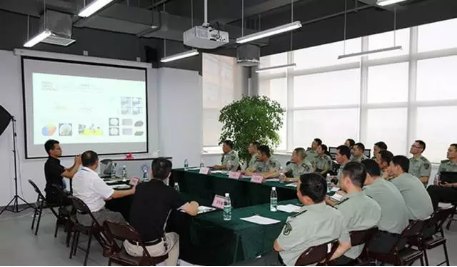
增(zēng)材製造將激發新型裝備設計理(lǐ)念,創造更加卓越的價值鏈體係。增材製造不(bú)僅是(shì)一種先進的製(zhì)造技術,它還將對現有的設計理念、生產方式和研發模式產生衝擊,使得製(zhì)造和設計被整合成為“精確研發”模式。這不但會影響(xiǎng)製造(zào)業本(běn)身,還將改(gǎi)變整個裝備研發體係。借助(zhù)信息技術所形成的“信息物理係統”,增材(cái)製造所具(jù)有的開放型和大眾性,將(jiāng)為未來(lái)的(de)創新搭建了廣闊的舞台。
上一篇:核(hé)工業的3D打印之路
下一篇:剖析粉末冶金技術的前世今生